Highly polished or orange skin Lunac 1
non-stick coatings on molds and rollers
The hardness, low surface energy / non-stick effect, corrosion resistance (e.g. to bio-degradable or water attracting plastics) and good cleaning capability of Lunac 1 is the main reason for Lunac 1 applications on molds and rollers. Additionally, in a spectacular short time Lunac 1 can be polished to a roughness of less than Ra = 0.02 µm (0.00079 mil), starting with a preceding roughness of Ra= 0.2 - 0.3 µm / 0.0079 - |
0.0118 mil. This reduces the mold's production costs significantly. The very dense micro crack free Lunac 1 surface is microscopically uniform and consequently also very suitable for optical applications (last figure). Like all Lunac versions, Lunac 1 can very well be applied locally. The substrate upper hardness limitation of HRc 50 should always be considered before Lunac 1 can be applied successfully. |
Highly polished surfaces
This female part of a soap dispenser (figure right) was locally plated with Lunac 1(bottom and middle part of the product forming part) to prevent the mold from corroding, caused by the corrosive action of the (water absorbing) ABS plastic. The mold below needed an extreme smooth scratch-resistant surface. This Lunac 1 coating could be finished to a final roughness as low as Ra= 0.005 µm / 0.0002 mil.
These two lamp cover molds display the 'flow polish' effect clearly. The left mold shows a surface before 50 µm (0.002") Lunac 1 coating was deposited. The manufacturer stated a good surface finish with the uncoated steel part was not feasible and the products gradually became dull. Lunac 1 is able to level out scratches to a depth of 10 µm / 0.00039" by the 'flow polish' effect and nearly eliminates the effect of the surface to become dull as result of usage.
Half dome surfaces (Lunac 1 RAD)
Especially perpendicular release can be facilitated by a macroscopically half dome
structure if the coinciding higher roughness (+/- Ra 0.6 µm) is allowed or desired. Especially
rollers and many extrusion dies proved to benefit from this effect in an unparalleled manner.
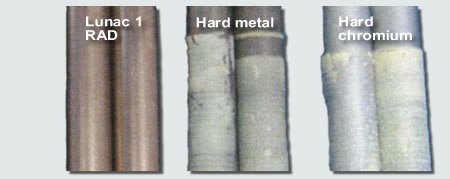
Guide rollers for yarn/thread production often suffer from thread wear scaling.
Under similar conditions, RAD Lunac 1 showed the most radical improvement. |
Mold size corrections
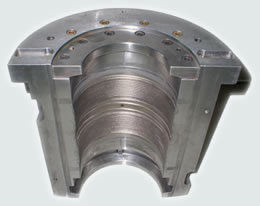